
The purpose of this blog is SAP S/4 HANA Production Planning & Manufacturing Integration with
Material Management
Finance and Controlling
Sales & Distribution
Production
1. Material Management
1.1 Create Purchasing Group
In this step, you can create and change purchasing groups. A purchasing group can be an individual or a group of individuals


1.2 Define Purchasing Document

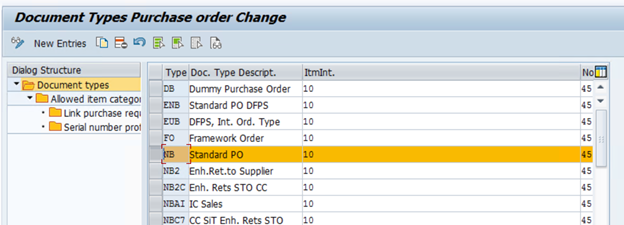
Finance Accounting & Controlling
2.1 Define field Status Variant


2.2 Define Posting Period Variant
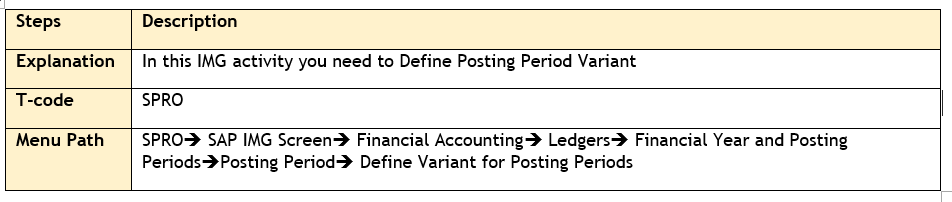

2.3 Open and Close Posting Period

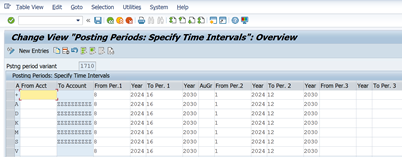
2.4 Enter Global Parameters
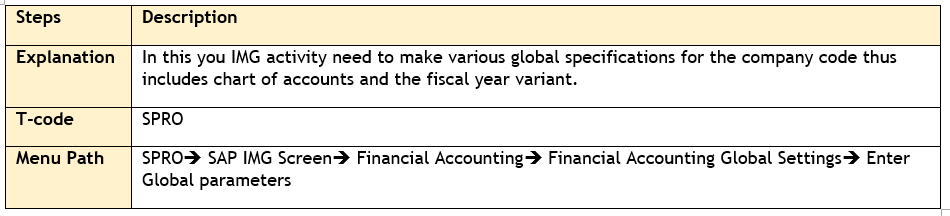

2.5 Create G/L Account with reference
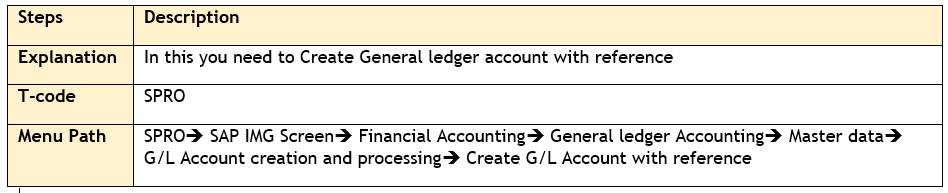

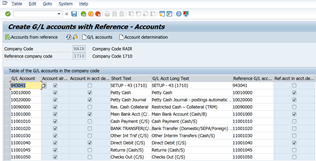
Click on account determination

2.6 Maintain Controlling


3. Material Management
3.1 Configure Automatic Account Determination
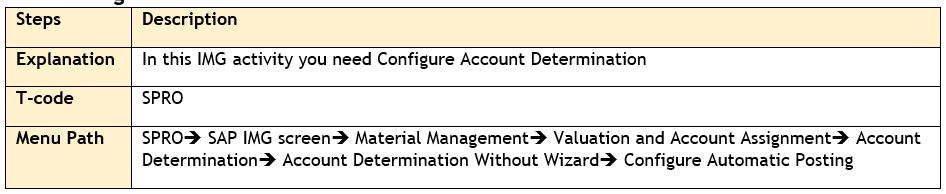


3.2 Define Valuation control
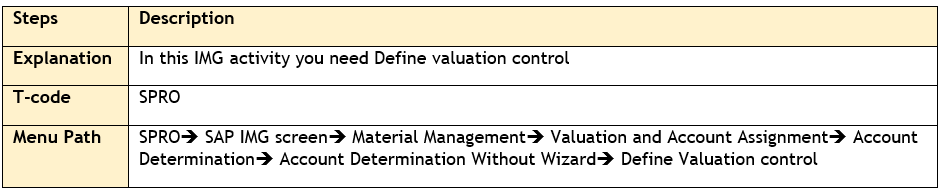

3.3 Group together Valuation area

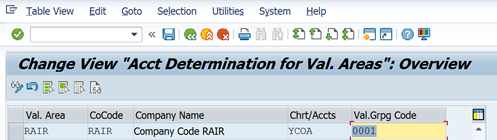
3.3 Maintain Company code to Material Management
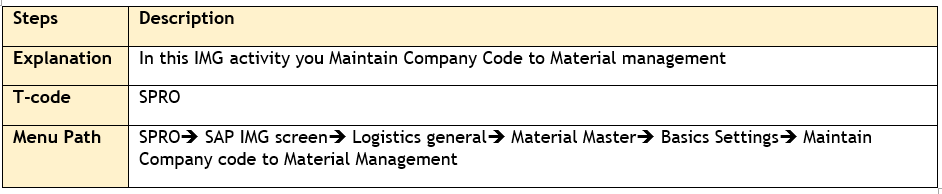

3.4 Define Attributes to Material Type

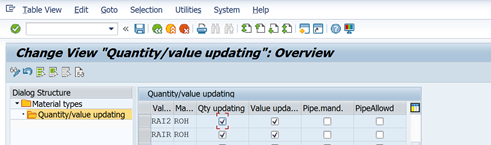

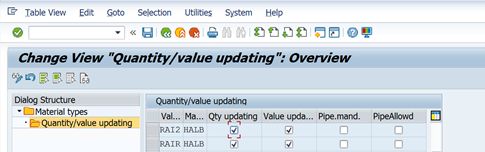


3.5 Assign Currency Type and Define Material Ledger type
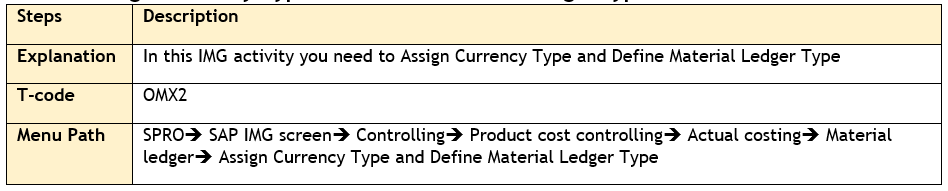

3.6 Assign Material Ledger Type to Valuation Area

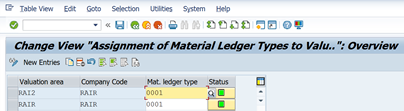
3.7 Activate Material Ledger Type to Valuation Area

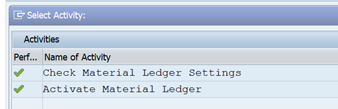
Activate Material ledger

3.7 Make Material Ledger Productive to Plant
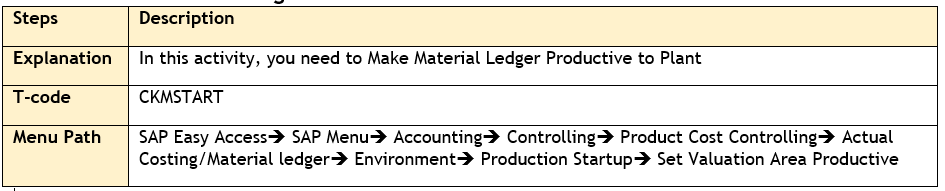


Sales & Distribution
4.1 Define Common Distribution channel


4.2 Define Common Division


4.3 Define Sales Document






4.4 Assign Sales Area to Sales Document type

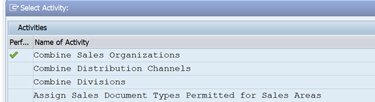
Combine Sales organization

Combine Distribution Channel

Combine Division

Assign Document Type Permitted Sales Area

4.5 Define and Assign Pricing Procedure

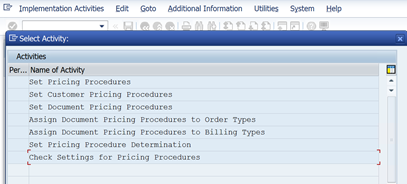
Set Pricing Procedure

Set Customer Pricing Procedure

Set Document Pricing Procedure

Assign Document Pricing Procedure to Order Type

Assign Document Pricing Procedure to Billing Type

Set Pricing Procedure Determination
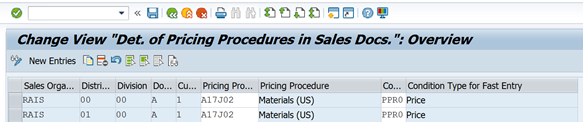
4.6 Define Item Category


4.7 Define Item Category Group


4.8 Assign Item Category
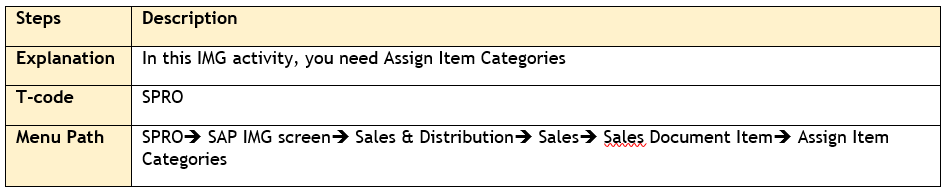

4.9 Define Delivery Type

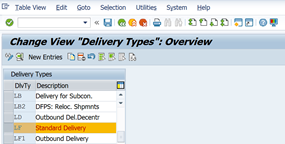



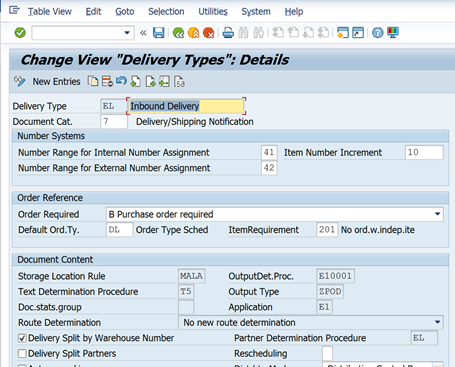
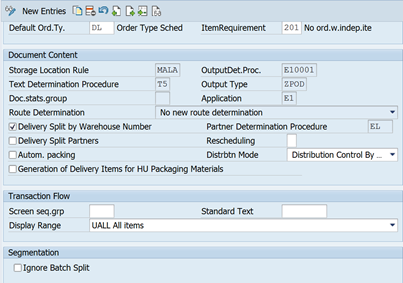
Production
5.1 MRP Controllers
MRP Controllers can be an individual role or group of rules performing the same task. It’s defined based on the role, responsibilities, or area of work instead of individuals.
The MRP controller is primarily responsible for attending to the requirements of materials.
MRP Controller is assigned to MRP 1 view of the material master.
This MRP controller can be used as one of the selection criteria when we run several reports.

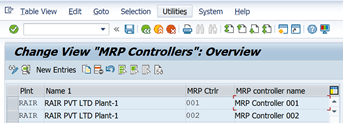


Note: MRP Controller is not only used in Production Planning, also used in Procurement Planning in Material Management.
5.2 Capacity Planner
The capacity planner or capacity planner group is responsible for evaluating the current work center or resource capacity. If required leveling of capacity can be performed.
The capacity planners are assigned in the capacity header data of the work center or resource.
This can be utilized as one of the selection criteria in all capacity evaluation & leveling reports.


5.3 Production Scheduler
The production scheduler is responsible for ensuring that production execution & operations take place as per the production plan.
Production schedulers can be assigned in the work scheduling view of the material master.

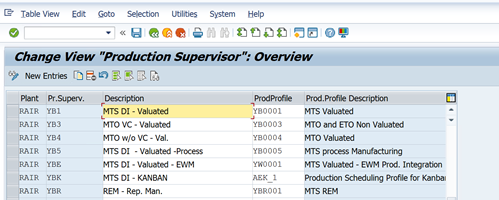

SAP Calendar
For planning & scheduling to effectively take place, it’s imperative that a calendar exists in the system.
This calendar is assigned to the plant.
The SAP Calendar creation function includes three individual steps:
Defining Holidays
Creating holiday calendar
Defining a factory calendar and assigning a holiday calendar to it.


Public Holiday

Holiday Calendar
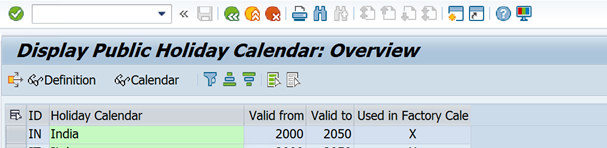
Factory Calendar

Conclusion
The above steps need to be followed to integrate Production with Material Management, Finance & Controlling, Sales Distribution & Distribution Modules.
Rajesh Sharma
SAP WM/EWM Functional Consultant
§ Linked in profile: https://www.linkedin.com/in/rajesh-sharma-204910278/
§ Twitter: RajeshS98151512/ RAJESH SHARMA@RAJESHS21287609
§ SAP Blogs: https://www.sastrageek.com/blog
Comments